Technology

The Bone Printing Solution
Ossiform® is founded on a worldwide IP protected technology developed in 2015.
Our solution is a bio-ink composed of powder particles suspended in a solid but meltable fatty acid matrix. The bio-ink enables a new 3D additive manufacturing process where objects are constructed directly from a computer-aided design (CAD) file.
The bio-ink is loaded into a syringe, heated to its melting point and extruded as a thin line onto a cooler stage on which it re-solidifies. The fatty acid is then removed through burning and the powders are sintered together.
Good Preclinical Proof
Good preclinical proof demonstrates that the P3D Bone implants perform as well as predicted.
- The implants are mechanically strong and free from contaminants,
- support the rapid formation of new vascularized bone,
- integrate with neighboring bone in vivo, and
- show clear signs of implant resorption and no signs of infection.
These results have been published in well-recognized scientific papers (See Publications section below).
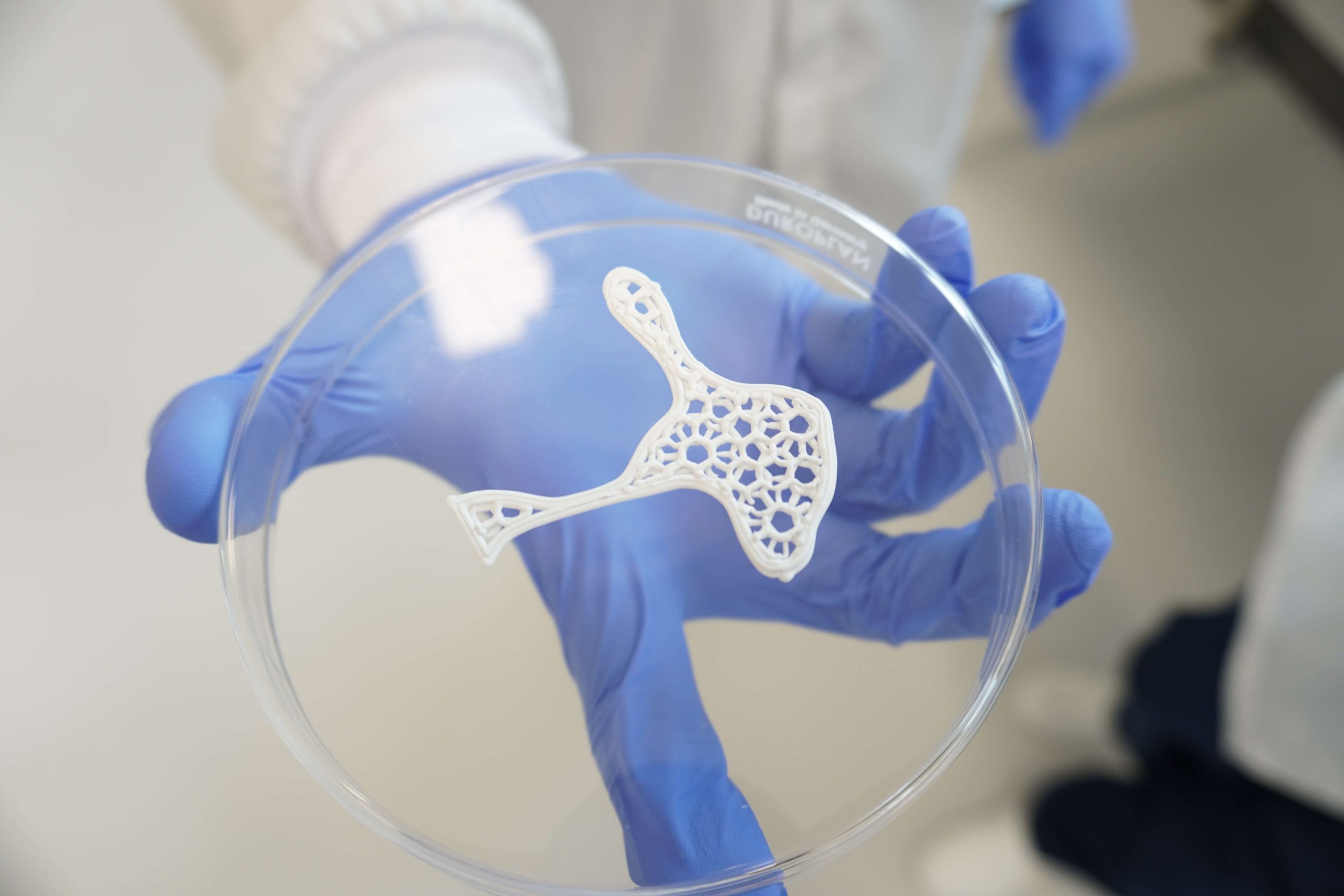
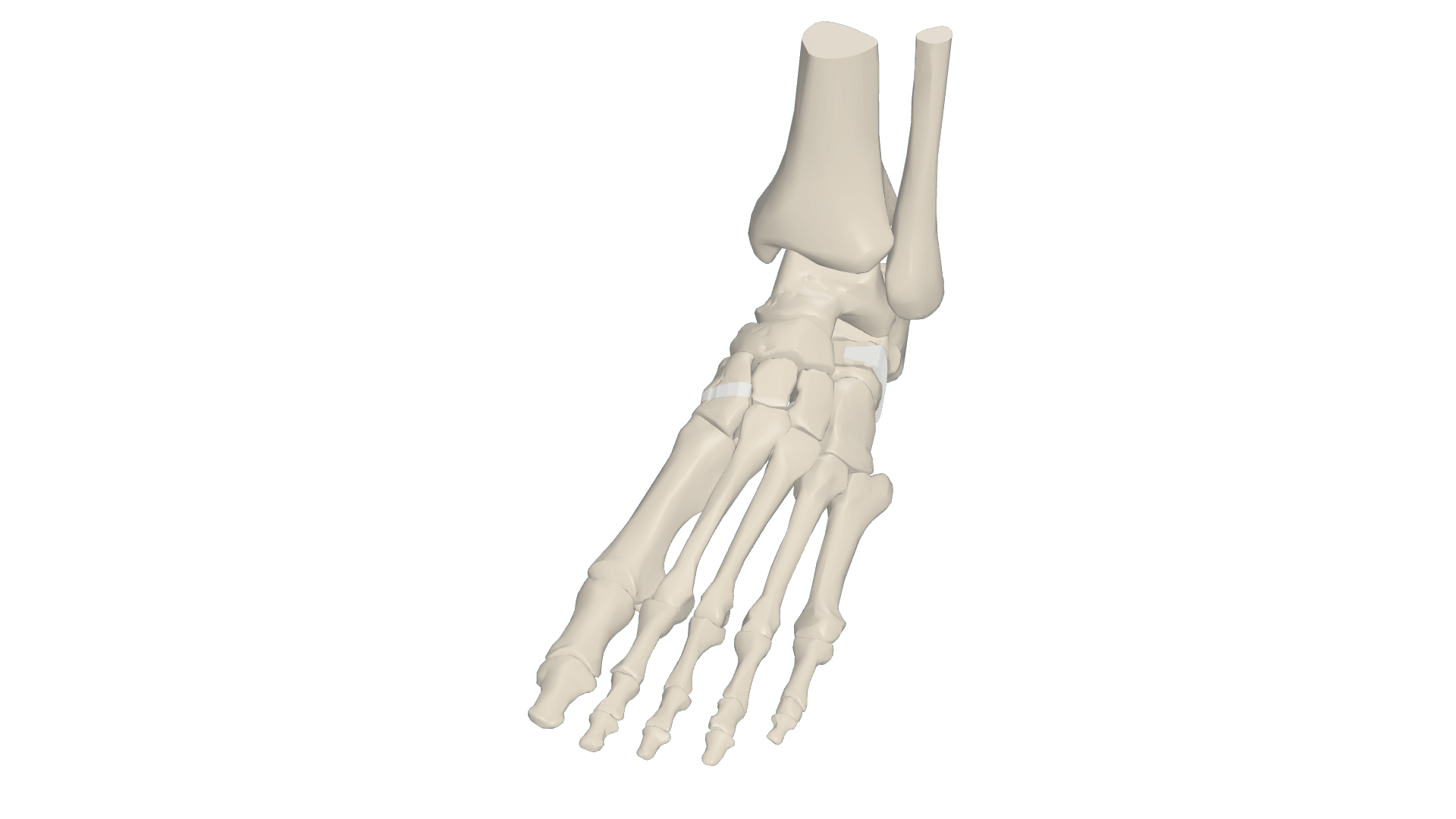
Ossiform’s technology will allow surgeons to reconstruct bone without the complications of foreign body implantation or the graft quality variability of allografts
We work in close collaboration with surgeons to provide bone graft substitutes that are optimized for the specific demands of diversified clinical applications, with an aim to improve bone healing outcomes and minimize the risk of complications and revision surgeries in orthopedic surgery and spinal fusion.
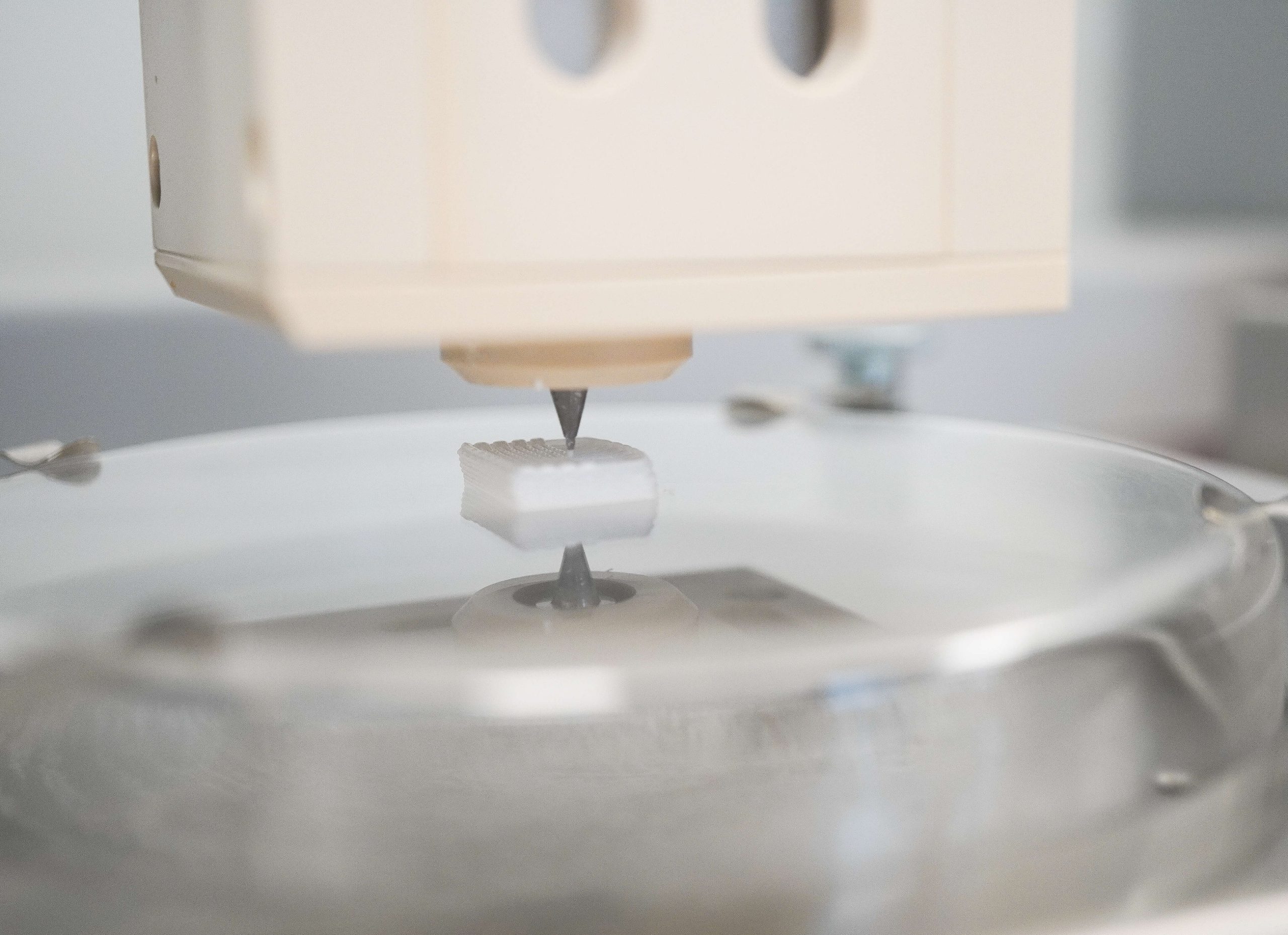
Publications
Thygesen, T., et al. Comparison of off-the-shelf β-tricalcium phosphate implants with novel resorbable 3D printed implants in mandible ramus of pigs. Bone (2022): 116370.
Get access here
Jensen MB, et al. Treating mouse skull defects with 3D printed fatty acid and tricalcium phosphate implants. Journal of Tissue Engineering and Regenerative Medicine. (2020): 1-11
Get access here
Jensen MB, et al. Composites of fatty acids and ceramic powders are versatile biomaterials for personalized implants and controlled release of pharmaceuticals. Bioprinting 10 (2018): e00027
Get access here
Slots C, et al. Simple additive manufacturing of an osteoconductive ceramic using suspension melt extrusion. Dental Materials 33.2 (2017): 198-208.
Get access her
Jensen MB et al. The performance of a new generation of 3D printed and drug and stem cell loaded implants in vitro and in vivo. DASCS2017 Stem Cell Conference. 2017.
See poster
Sascha Senck, et al. Ceramic additive manufacturing and microstructural analysis of tricalcium phosphate implants using X-ray microcomputed tomography. Open Ceramics (2024): 100628.
Get access here